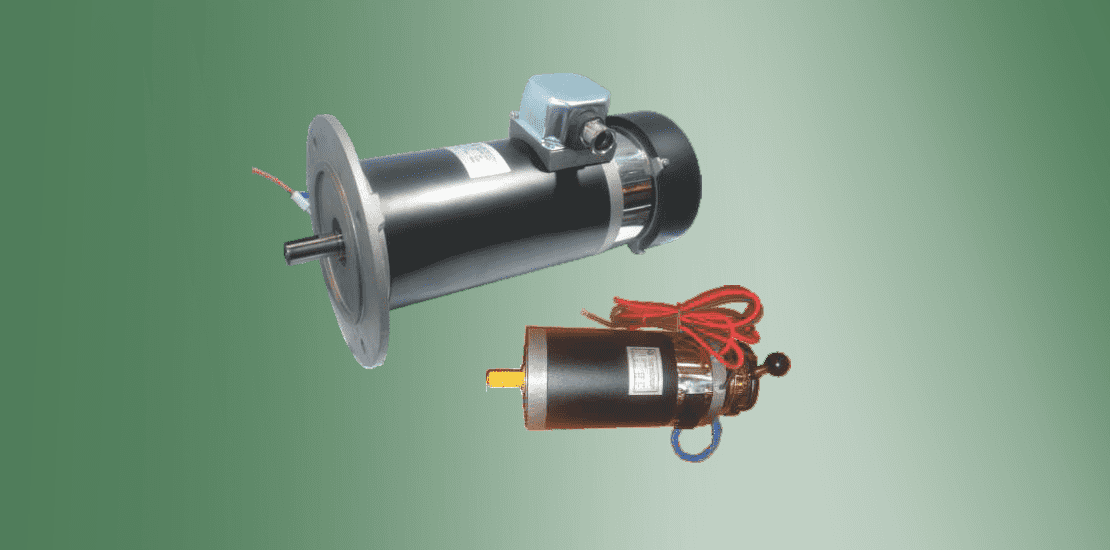
Reviewing the Service History:
D.C. motor maintenance, as with all types of industrial maintenance, requires pre-maintenance planning and scheduling. This starts with reviewing the motor’s service history usually contained within an equipment maintenance log or, if the log is not available, interviewing the customer, operator or responsible party to determine what type of maintenance is required, preventative or corrective (failure repair).
7 The goal is to determine:
- What kind of maintenance is required.
- What maintenance personnel are needed to perform the maintenance (skill level).
- What parts are needed to complete the maintenance (i.e., bearings, brushes, etc.)
- What kind of scheduling or coordination with other departments is required to perform the maintenance (downtime or off-hours scheduling)
- What kind of safety hazards exist that would interfere with the maintenance.
If there are problems other than the motor itself that caused the motor breakdown.
Noise and Vibration Inspections:
Noises and vibrations are not limited to mechanical problems or imbalances; electrical imbalances, such as open or shorted winding or uneven air gaps, can cause noises or vibrations. The easy way to troubleshoot an electrical from an mechanical imbalance is to first power up the motor, then disconnect power. If the noise/vibration exists while it is unpowered, the problem is mechanical; if the noise stops while power is disconnected, the problem is usually electrical.
Visual Inspections:
A visual inspection is meant to observe and record anomalies about the physical condition of the motor in a de-energized state. A motor that appears dirty, corroded or has the “beat up” look indicates that it was operated in a rough environment and may have more problems than usual. This inspection should include the “smell” test. Is there a burned odor coming from the motor windings? The burnt smell is coming from the insulation varnish of the motor windings. 12 If so, this suggests an overheating problem. Motor winding damage is possible under these conditions so winding tests should be conducted.
Bearings: Replacement and Lubrication
Lubrication is only one of three maintenance tasks involved with motor bearings. Cleaning, removal and replacement are the other tasks. In the noise and vibration inspections, the bearings should have been inspected for abnormal noises, vibrations or hot bearings. The “feel” and “sound” tests are simple methods to gauge bearing condition. 29 For the “feel” test, with the motor running, touch the bearing housing. If it is very hot to the touch, the bearing is probably malfunctioning. In the “sound” test, listen for thumping or grinding noises. If they exist, the bearings need a closer look and possible replacement. For most types, the sources of bearing failures are:
- Insufficient oil or grease.
- Too much grease causing churning and overheating.
- Worn bearings (i.e., broken balls or rough races, etc.)
- Hot motor or external environment.
If the service history demonstrates repeated bearing failures, check the manufacturer’s specifications to determine if the correct bearing has been installed. If that’s not the case, then an external factor could be the cause.